Top Five All-Electric Injection Moulding Myths: Getting Real About Reliability And Repairs
All-electric injection moulding machines have many excellent qualities, including greater precision, higher power density and lower carbon emissions. Yet there’s a preconception that these systems are more expensive to repair. Ashlee Gough, Area Sales Manager at Sumitomo (SHI) Demag UK delves into and discredits the top five myths regularly encountered.
- Capacity planning is a moving target
Struggling to stay on top of everything is one of the greatest challenges for production engineers. Yet, Mean Time Between Failure (MTBF) is one of the simplest reliability measurements for polymer processors. It is also probably the most valuable KPI for equipment-reliant operations as it provides an accurate method for measuring machine availability, and helps with the planning of maintenance schedules, as well as capacity planning.
With fewer moving and wear parts, the time-lapse between one failure to the next is significantly less on all-electric moulding machines. Proving this, a study of the overall machine MTBF on a Sumitomo (SHI) Demag IntElect2 under warranty was on average 4.4 years – double that of an equivalent hydraulic machine.
This MTBF metric is not just attributed to the machine design, but also how well an operative repeatedly handles or interacts with this valuable asset. A poorly executed repair job or implementing a quick fix and running the machine until it finally goes bump can just as easily result in a low MTBF result.
2. Same or similar service time
Electric machines are less mechanically complex. With no flexing of hoses, no sensitive valves, perishable seals or hydraulic fluid, the risk of an emergency callout is significantly lower.
Studies conducted by Sumitomo (SHI) Demag revealed that a 130 ton hydraulic machine operating 24/5 needed 39 hours of routine service work, compared to just six hours for an equivalent IntElect2 model.
Analysing and treating oil in order to maintain its optimum properties, as well as changing the oil filter, are essential routine maintenance task on hydraulic systems. The timing of these tasks are critical and any delay or neglect can drastically increase the risk of machine failure. Performing a filter change to the proper standards realistically takes a couple of hours. If an oil change or complete flush through is required, this not only results in unplanned downtime but also comes at a great expense.
Additionally, hydraulic hoses should be regularly inspected. It is recommended that they are replaced every ten years. Contamination and airlocks are always a danger when replacing hydraulic hoses. Because of this, it is recommended that this work should be undertaken by a professional.
Hydraulic machines with accumulator technology should ideally have the bladder replaced periodically. Inspecting the accumulator housing for cracks every ten years using x-ray is equally advisable.
3. Drives are expensive to repair
Typically, all-electric machines have the reputation of being expensive to repair when they go wrong. This view is often based on the cost of replacing an entire drive system.
Many moulding machine suppliers source their all-electric drives from external OEMs, which makes it more challenging to source component replacements, exchange or access service support. In the best-case scenario, moulders might be able to source and switch out a power or control module. Yet in most instances, sourcing a new complete drive is the reality, which of course, runs at a premium cost.
That’s one of the key reasons why Sumitomo (SHI) Demag has an R&D centre dedicated to drive development and designs and builds its own drive motors, designed purely for injection moulding machines, in-house. Being able to source individual replacement boards is a more sustainable solution for customers. Spares are also held for immediate shipment.
Drives that are designed to be modular are also much more cost efficient. Why replace three power modules, when you can replace just the one that’s failed? It can be the difference between several hundred pounds and a quick fix, rather than a complete drive replacement which could run into a few thousand.
4. Infrastructure savings takes a long time
The savings when switching to all-electric are instant and can often be significant. Because each axis of an all-electric injection moulding machine is independently controlled, parallel functions are possible. This means that they can perform multiple tasks at once, for example ejection during mould opening or ejector retraction during mould closing. Resulting in faster cycle times which significantly increases productivity, output and component quality.
The increased efficiency delivered by direct drives means that they use considerably less energy than hydraulic machines – in the case of the IntElect between 40% and 85% less than conventional solutions. As electric drives generate less heat than their hydraulic
counterparts, they require less cooling than conventional machines of a similar size. Additionally, the recovery of kinetic energy while the clamping unit is braking generates energy which can be used for plastification.
This not only reduces the burden on existing infrastructures but also lessens the investment when building or relocating to new premises.
5. Wear and tear is a guessing game
Reducing costs, risks and disruption are high on the priority list of many moulders aiming to achieve optimum processing efficiency, with machine reliability being the most influential factor.
Regardless of machine type, it is imperative to monitor and routinely service moving parts, e.g. toggle systems, seals or bearings, which are subjected to varying degrees of wear and tear.
It is often easy to identify wear on mechanical components via sensory diagnosis – surfaces may appear worn/scored, it may sound out of place or it may smell “hot”. However, electrical systems can often be overlooked as it can be very difficult to diagnose wear on electrical components such as electrical drives, motors, contactors, relays and PCBs. A moulder often won’t be aware of an issue until the machine stops. Thermal imaging offers a big advancement in this area.
Regular thermal imaging checks of electrical cabinets can give an early indication of impending component failure and are a quick and cost-effective way to spot potential issues early on.
The use of thermographic equipment for condition monitoring is included in Sumitomo (SHI) Demag’s annual activeCare check. Rather than a ‘best guess’ diagnosis, activeCare engineers can assess the collected data and determine when equipment or parts are likely to fail in service.
The biggest mistake moulders can make is discounting high-performance all-electric machines on price alone. The price difference between hydraulic and all-electric injection moulding machines has dropped considerably over the past 15 years. When considering the potential energy savings, productivity improvements and prolonged reliability, further total cost of ownership savings can be realised.
For all-electric machine service costs, the studies speak volumes with the facts outweighing the fiction.
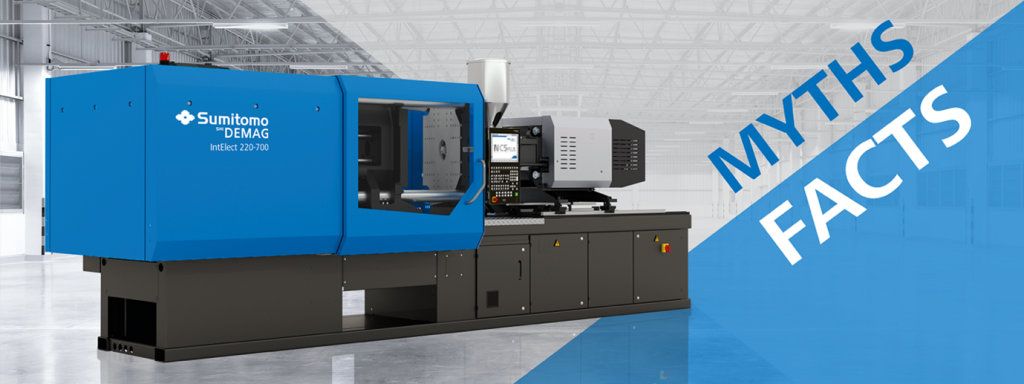
Ashlee Gough from Sumitomo (SHI) Demag UK dispels 5 misconceptions about all-electric moulding machine costs.
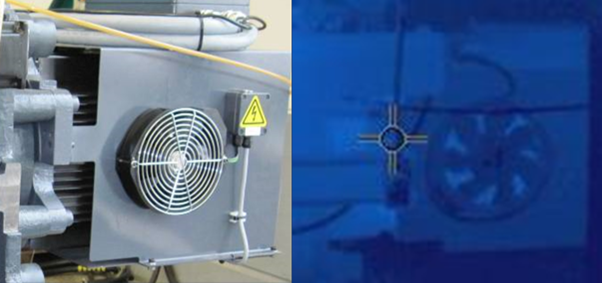
Thermal imaging a direct drive can provide a good indicator of any inefficiencies, heat emissions and even wear and tear.